EDM (Electro Discharge Machining) Wire Erosion is a precision engineering process where a work piece is cut through with a strand of wire, it creates electrical sparks between the wire and the work piece, and these electrical sparks cut the work piece. It is a cost-effective method that has incredible accuracy on thicker component parts. Wire cutting machines can cut complex shapes even in tough materials.
The sparks are extremely controlled and in the more recent years to make sure that the cutting is accurate, dielectric deionised water is used. The water acts as a coolant to make sure the metal components do not overheat and to wash away any particles that could get in the way. The wire erosion process starts towards the edge of a work piece or by drilling a hole where the process will start.
The EDM wire erosion process dates to 1770 when an English scientist, Joseph Priestley discovers that electrical discharge could erode metal.
Advantages:
- You can achieve very intricate detail when using this form of machinery.
- Hard materials do not affect the process.
- It can handle even the smallest of workpieces compared to the more traditional cutting tools which cause damage.
- There is not any direct contact between the tools and workpiece, meaning weaker materials can be machined without it breaking.
- Any surface finish can be obtained.
- Fine holes can easily be drilled.
- Complex cutting can be achieved.
- Wire Erosion does not leave burrs.
Disadvantages:
- The materials used must be conductive.
- It can be the more expensive option when compared with CNC milling.
Material Suitable
There are many different types of metals that can be used in the wire erosion process. The typical options of metal electrode are:
Brass:
It has a high rate of wear however it is primarily now used for EDM hole drilling.
Tellurium Copper:
The metal removal rate and the wear are both reasonable.
Copper Tungsten:
Used when the safety of copper is needed, however, this material has a much better wear resistance due to its high melting point.
Silver Tungsten:
If you need a high conductivity level that silver offers but with the added resistance of Tungsten. This is a more expensive option compared to Copper Tungsten and it is only used for specific applications.
Tungsten:
This is not a common choice; it is used when speed isn’t considered a necessity for a job. Tungsten will work slower than other metals. Using Tungsten is more expensive.
Evaluation of Wire Erosion
Overall, the wire erosion process will create your product from a workpiece with ease but without touching it so no matter how thin or fragile the workpiece, it won’t get damaged. If you would like any more information regarding our Wire Erosion services here at REV1 Precision Engineering, get in touch with our helpful team today.
Why Choose Us?
Highly Experienced Professionals – wire erosion is a process that requires a lot of finesse and precision. We have a team of experts who are highly skilled and experienced and can guarantee you the best results regardless of how complex your requirements may be.
Compatible with a wide collection of materials – our wire cutting services are available for all components and parts that are made from a wide variety of materials which include steel, tungsten, copper, brass and aluminium.
Bespoke Solutions – No matter how complex your requirements or the cut might be, our wire erosion services are able to achieve that and more. Because in this case, the wire does not actually touch the material being cut, we are able to preserve the material even if it is fragile and it will not get damaged. We are also able to work on thick pieces.
Highly Precise – to make the cuts even more precise, we use dielectric deionized water which acts as a coolant to prevent the components from overheating and washes away particles that could compromise the integrity of the cut. Using this process, we can guarantee extremely accurate results to our clients.
EDM WIRE EROSION CAPABILITY
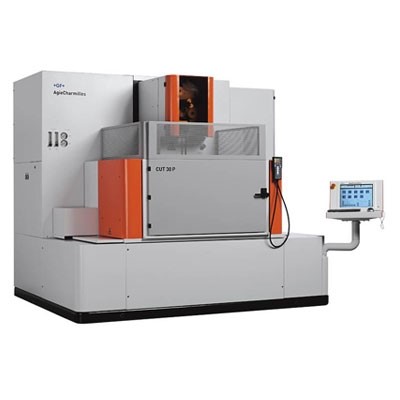
GF Agie Charmilles EDM Cut 30P EDM
X AXIS TRAVEL: 600 mm
Y AXIS TRAVEL: 400 mm
Z AXIS TRAVEL: 350 mm